A New Woody Flavour from Cloudy Bay Winery
Cloudy Bay, producers of world-renowned wines in New Zealand’s Marlborough region, has recently extended operations with an all timber-bottling hall. Employing the combined skills of architect Les Morris and engineer Graham Kerrigan of Kerrigan Engineers, Cloudy Bay Winery now boasts a people friendly bottling hall with a rustic charm that is faithful to its original setting.
The bottling hall was not the first time that Cloudy Bay had brought Morris and the primarily sole operator, Kerrigan, together. The two had previously combined forces on other Cloudy Bay projects. As the entire wine industry in Marlborough, at the top end of New Zealand's south island, has boomed in the last decade, most small-scale wineries have been seeking to expand operations. Cloud Bay was no exception. Having been around for approximately 5 years, the winery is now undergoing its own program of expansion.
CHALLENGE
Cloudy Bay came up with a revolutionary idea for their cellar and press. While pricked grapes are ordinarily lifted into large cylinders for pressing, Cloud Bay wanted a press basin built into holes in the ground for easier use. Kerrigan and Morris worked on this mostly structural project and also on a cellar for wine storage, with stainless steel tanks each with an 80,000-litre capacity. From there the architect and engineer team moved onto the bottling hall, involving Futurebuild® LVL in the project.
The hall building is 20 metres wide by 43 metres long, with portals at 5.4 metre centres, as specified by Futurebuild LVL. The building itself is constructed using tilt slab, pre-cast concrete walls. Morris and Kerrigan favoured this method for both aesthetic and practical reasons.
In order to fit in with the look of the winery, the pair wanted to give the hall a permanence and quality that could not be achieved using a tin shed or other similar construction. The aesthetics also need to be consistent with the pre-existing rustic charm of the winery. Says Morris, they wanted to get away from the industrial look of steel and the blandness of only concrete. Kerrigan suggested the alternative of timber portals and Futurebuild in turn suggested the Futurebuild LVL products. Both for aesthetic reasons but also because it was economically viable due to simpler construction, Futurebuild LVL was the material chosen.
SOLUTION
hySPAN® and hy90® timber was chosen with the comfort of the winery’s people in mind. As opposed to the cellar where the wine is stored, the hall is where the people work. For this reason the internal space needed to be people-friendly and Cloudy Bay felt that timber, its warmth and its appearance was far more pleasant than a steel frame. Another significant advantage of the hySPAN and hy90 beams was dust prevention. With steel I beams, the I-beam has a ledge that tends to collect a lot of dust, which was of concern to Cloudy Bay. As the hySPAN beams have no ledges, but rather are rectangular shaped with very sharp and clean lines, there are no ledges for the dust to collect on when the wind blows through the building. “Dust is the last thing Cloudy Bay wanted…they didn’t want cloudy wine from Cloudy Bay,” says Morris.
RESULT
The final bottling hall has indeed met all of Cloudy Bay’s expectations. While Cloudy Bay had wanted timber, the Glulam was too expensive, whereas the Futurebuild LVL structure had the right look but also came in at the right price. Both visually and structurally, the hall matches the existing buildings and is comfortable and workable for both the winery’s product and its people.
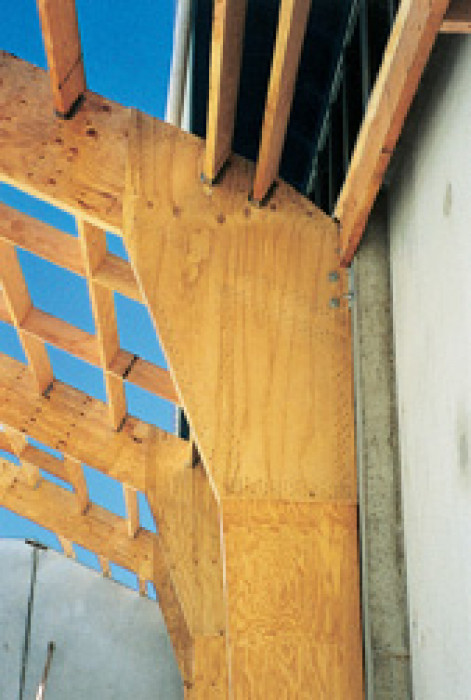
PRODUCTS:
hySPAN® & hy90®
DESIGNER & TIMBER ENGINEERING:
Timberbuilt
BUILDER:
Mick Neale
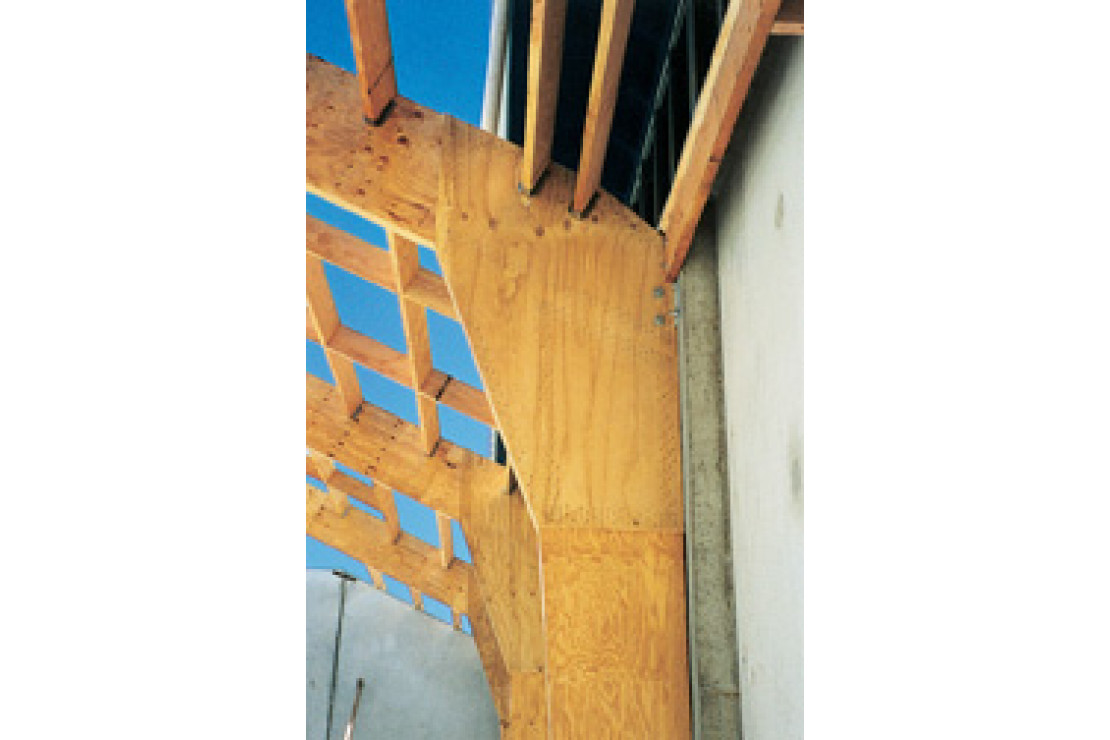
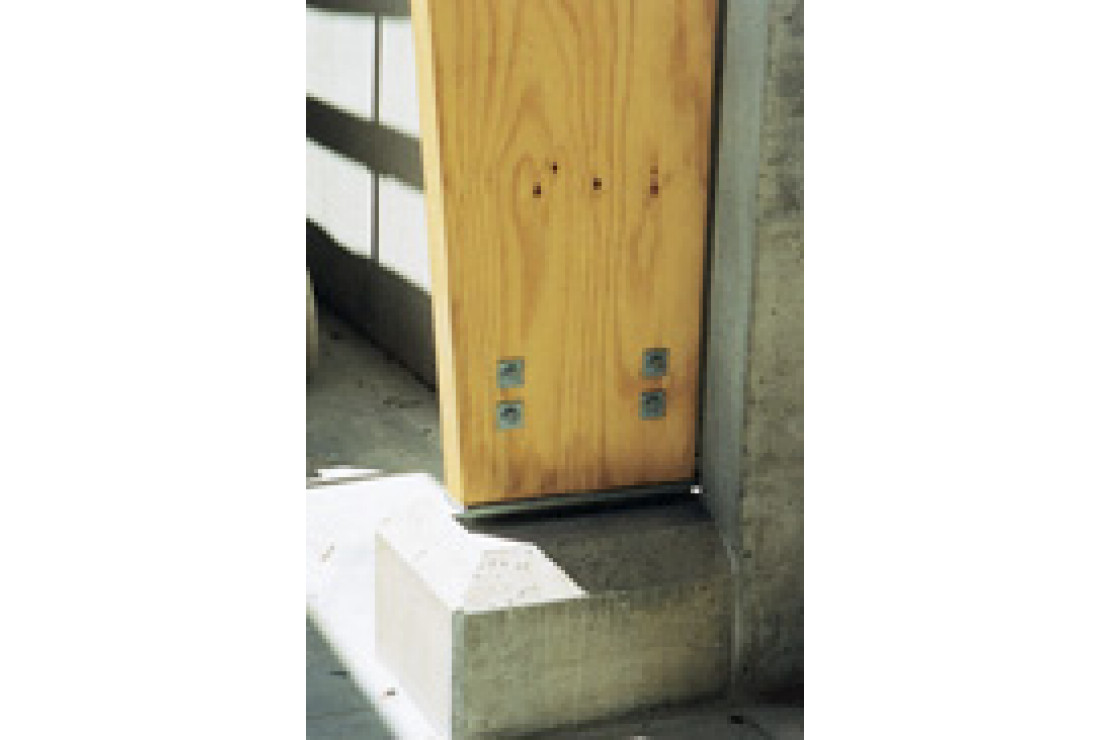
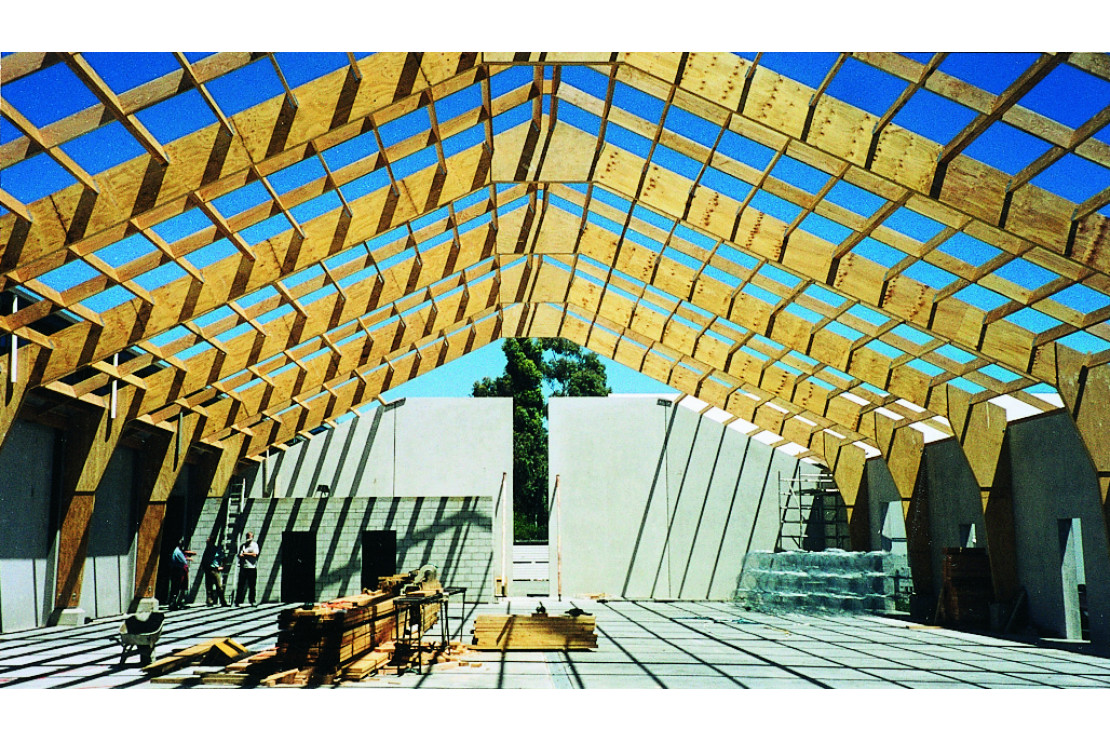